ਮੋਲਡ ਕੀਤੇ ਹਿੱਸਿਆਂ ਵਿੱਚ ਕਾਲੇ ਚਟਾਕ ਜਾਂ ਕਾਲੇ ਸ਼ਾਮਲ ਕਰਨਾ ਇੱਕ ਤੰਗ ਕਰਨ ਵਾਲੀ, ਸਮਾਂ ਬਰਬਾਦ ਕਰਨ ਵਾਲੀ, ਅਤੇ ਮਹਿੰਗੀ ਸਮੱਸਿਆ ਹੈ।ਉਤਪਾਦਨ ਸ਼ੁਰੂ ਕਰਨ ਵੇਲੇ ਅਤੇ ਪੇਚ ਅਤੇ ਸਿਲੰਡਰ ਦੀ ਨਿਯਮਤ ਸਫਾਈ ਤੋਂ ਪਹਿਲਾਂ ਜਾਂ ਦੌਰਾਨ ਕਣ ਛੱਡੇ ਜਾਂਦੇ ਹਨ।ਇਹ ਕਣ ਉਦੋਂ ਵਿਕਸਤ ਹੁੰਦੇ ਹਨ ਜਦੋਂ ਸਮੱਗਰੀ ਓਵਰਹੀਟਿੰਗ ਕਾਰਨ ਕਾਰਬਨਾਈਜ਼ ਹੁੰਦੀ ਹੈ, ਜੋ ਉਦੋਂ ਹੋ ਸਕਦੀ ਹੈ ਜਦੋਂ ਮਸ਼ੀਨ ਵਿੱਚ ਤਾਪਮਾਨ ਨੂੰ ਘਟਾਏ ਬਿਨਾਂ ਸਮੱਗਰੀ ਦੇ ਪ੍ਰਵਾਹ ਨੂੰ ਲੰਬੇ ਸਮੇਂ ਲਈ ਰੋਕਿਆ ਜਾਂਦਾ ਹੈ।
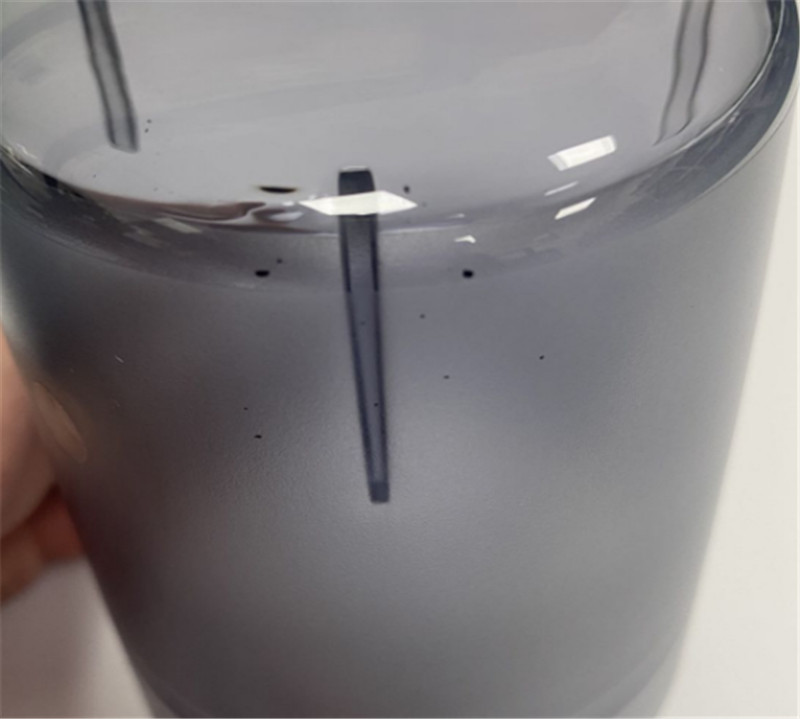
ਕਾਲੇ ਚਟਾਕ ਦੇ ਕਾਰਨ
ਰਾਲ ਸੜਨ
ਕਿਉਂਕਿ ਪਲਾਸਟਿਕ ਸਮੱਗਰੀ ਇੱਕ ਰਸਾਇਣਕ ਹੈ, ਇਹ ਹੌਲੀ-ਹੌਲੀ ਸੜ ਜਾਂਦੀ ਹੈ ਜਦੋਂ ਇਹ ਪਿਘਲਣ ਵਾਲੇ ਬਿੰਦੂ ਤੋਂ ਉੱਪਰ ਗਰਮ ਕੀਤੀ ਜਾਂਦੀ ਹੈ।ਤਾਪਮਾਨ ਜਿੰਨਾ ਜ਼ਿਆਦਾ ਹੁੰਦਾ ਹੈ ਅਤੇ ਜਿੰਨਾ ਜ਼ਿਆਦਾ ਸਮਾਂ ਹੁੰਦਾ ਹੈ, ਓਨੀ ਹੀ ਤੇਜ਼ੀ ਨਾਲ ਸੜਨ ਦੀ ਪ੍ਰਕਿਰਿਆ ਹੁੰਦੀ ਹੈ।ਇਸ ਤੋਂ ਇਲਾਵਾ, ਬੈਰਲ ਦੇ ਅੰਦਰ, ਅਜਿਹੇ ਖੇਤਰ ਹੁੰਦੇ ਹਨ ਜਿੱਥੇ ਰਾਲ ਆਸਾਨੀ ਨਾਲ ਬਰਕਰਾਰ ਰਹਿੰਦੀ ਹੈ, ਜਿਵੇਂ ਕਿ ਚੈੱਕ ਨਾਨ-ਰਿਟਰਨ ਵਾਲਵ ਅਤੇ ਪੇਚ ਥਰਿੱਡ।ਇਹਨਾਂ ਹਿੱਸਿਆਂ ਵਿੱਚ ਜੋ ਰਾਲ ਬਚੀ ਰਹਿੰਦੀ ਹੈ, ਉਹ ਸੜ ਜਾਂਦੀ ਹੈ ਜਾਂ ਕਾਰਬਨਾਈਜ਼ਡ ਹੋ ਜਾਂਦੀ ਹੈ, ਅਤੇ ਫਿਰ ਮੋਲਡ ਕੀਤੇ ਉਤਪਾਦ ਵਿੱਚ ਮਿਲਾਉਣ ਲਈ ਤਾਲ ਨਾਲ ਡਿੱਗ ਜਾਂਦੀ ਹੈ, ਇਸ ਤਰ੍ਹਾਂ ਕਾਲੇ ਧੱਬੇ ਬਣ ਜਾਂਦੇ ਹਨ।
ਨਾਕਾਫ਼ੀ ਸਫਾਈ
ਇਹ ਤੱਥ ਕਿ ਪਹਿਲਾਂ ਵਰਤੀ ਗਈ ਰਾਲ ਸਫ਼ਾਈ ਨਾ ਹੋਣ ਕਾਰਨ ਮੋਲਡਿੰਗ ਮਸ਼ੀਨ ਵਿੱਚ ਰਹਿੰਦੀ ਹੈ, ਇਹ ਵੀ ਕਾਲੇ ਬਿੰਦੀਆਂ ਦਾ ਇੱਕ ਕਾਰਨ ਹੈ।ਜਿਵੇਂ ਕਿ ਉਪਰੋਕਤ ਪੈਰੇ ਵਿੱਚ ਵਰਣਨ ਕੀਤਾ ਗਿਆ ਹੈ, ਕਿਉਂਕਿ ਅਜਿਹੇ ਖੇਤਰ ਹਨ ਜਿੱਥੇ ਰਾਲ ਆਸਾਨੀ ਨਾਲ ਬਰਕਰਾਰ ਰਹਿੰਦੀ ਹੈ, ਜਿਵੇਂ ਕਿ ਚੈਕ ਰਿੰਗ ਅਤੇ ਪੇਚ ਥਰਿੱਡ, ਸਮੱਗਰੀ ਤਬਦੀਲੀ ਦੇ ਦੌਰਾਨ ਇਹਨਾਂ ਖੇਤਰਾਂ ਵਿੱਚ ਇੱਕ ਅਨੁਸਾਰੀ ਤੀਬਰਤਾ ਅਤੇ ਸਫਾਈ ਦੇ ਸਮੇਂ ਨੂੰ ਲਾਗੂ ਕਰਨਾ ਜ਼ਰੂਰੀ ਹੈ।ਇਸ ਤੋਂ ਇਲਾਵਾ, ਹਰੇਕ ਸਮੱਗਰੀ ਲਈ ਢੁਕਵੀਂ ਸਫਾਈ ਵਿਧੀ ਨੂੰ ਨਿਯੁਕਤ ਕੀਤਾ ਜਾਣਾ ਚਾਹੀਦਾ ਹੈ.ਸਮਾਨ ਰੈਜ਼ਿਨਾਂ, ਜਿਵੇਂ ਕਿ PC→PC, ਦੀ ਸਫਾਈ ਕਰਨਾ ਮੁਕਾਬਲਤਨ ਆਸਾਨ ਹੈ, ਪਰ ਜੇ ਇਹ ਵੱਖ-ਵੱਖ ਕਿਸਮਾਂ ਦੀਆਂ ਸਮੱਗਰੀਆਂ ਦੀ ਸਫਾਈ ਹੈ, ਕਿਉਂਕਿ ਪਿਘਲਣ ਦਾ ਬਿੰਦੂ ਜਾਂ ਸੜਨ ਦਾ ਤਾਪਮਾਨ ਵੱਖਰਾ ਹੁੰਦਾ ਹੈ, ਜਦੋਂ ਕਿ ਰੈਜ਼ਿਨਾਂ ਵਿਚਕਾਰ ਅਨੁਕੂਲਤਾ (ਅਨੀਅਤ) ਮੌਜੂਦ ਹੁੰਦੀ ਹੈ। , ਸਫਾਈ ਦੇ ਬਾਵਜੂਦ ਬਹੁਤ ਸਾਰੇ ਮਾਮਲਿਆਂ ਵਿੱਚ ਇਸਨੂੰ ਪੂਰੀ ਤਰ੍ਹਾਂ ਹਟਾਇਆ ਨਹੀਂ ਜਾ ਸਕਦਾ।
ਵਿਦੇਸ਼ੀ ਪਦਾਰਥਾਂ ਦਾ ਮਿਸ਼ਰਣ (ਗੰਦਗੀ)
ਕਾਲੇ ਧੱਬਿਆਂ ਦਾ ਇੱਕ ਕਾਰਨ ਗੰਦਗੀ ਵੀ ਹੈ।ਜੇ ਹੌਪਰ ਵਿੱਚ ਖੁਆਏ ਗਏ ਕੁਝ ਗੋਲੀਆਂ ਨੂੰ ਘੱਟ ਸੜਨ ਵਾਲੇ ਤਾਪਮਾਨ ਵਾਲੇ ਹੋਰ ਰੈਜ਼ਿਨਾਂ ਨਾਲ ਮਿਲਾਇਆ ਜਾਂਦਾ ਹੈ, ਤਾਂ ਰਾਲ ਦੇ ਸੜਨ ਕਾਰਨ ਕਾਲੇ ਚਟਾਕ ਆਸਾਨੀ ਨਾਲ ਪੈਦਾ ਹੋ ਸਕਦੇ ਹਨ।ਇਸ ਤੋਂ ਇਲਾਵਾ, ਰੀਸਾਈਕਲ ਕੀਤੇ ਪਲਾਸਟਿਕ ਵੱਲ ਧਿਆਨ ਦਿੱਤਾ ਜਾਣਾ ਚਾਹੀਦਾ ਹੈ।ਇਹ ਇਸ ਲਈ ਹੈ ਕਿਉਂਕਿ ਰੀਸਾਈਕਲ ਕੀਤੇ ਪਲਾਸਟਿਕ ਨੂੰ ਕਈ ਵਾਰ ਗਰਮ ਕੀਤੇ ਜਾਣ ਤੋਂ ਬਾਅਦ ਸੜਨ ਦਾ ਜ਼ਿਆਦਾ ਖ਼ਤਰਾ ਹੁੰਦਾ ਹੈ (ਦੁਹਰਾਈ ਜਾਣ ਵਾਲੀ ਰੀਸਾਈਕਲ ਦੀ ਵੱਧ ਗਿਣਤੀ, ਗਰਮ ਕਰਨ ਦਾ ਸਮਾਂ ਜਿੰਨਾ ਜ਼ਿਆਦਾ ਹੋਵੇਗਾ)।ਇਸ ਤੋਂ ਇਲਾਵਾ, ਰੀਸਾਈਕਲਿੰਗ ਪ੍ਰਕਿਰਿਆ ਦੌਰਾਨ ਇਹ ਧਾਤ ਨਾਲ ਦੂਸ਼ਿਤ ਹੋ ਸਕਦਾ ਹੈ।
ਕਾਲੇ ਚਟਾਕ ਲਈ ਹੱਲ
1. ਪਹਿਲਾਂ, ਉਦੋਂ ਤੱਕ ਚੰਗੀ ਤਰ੍ਹਾਂ ਧੋਵੋ ਜਦੋਂ ਤੱਕ ਕਾਲੇ ਧੱਬੇ ਹੁਣ ਦਿਖਾਈ ਨਹੀਂ ਦਿੰਦੇ।
ਕਾਲੇ ਚਟਾਕ ਬੈਰਲ ਵਿੱਚ ਚੈਕ ਰਿੰਗ ਅਤੇ ਪੇਚ ਥਰਿੱਡ ਵਿੱਚ ਰਹਿੰਦੇ ਹਨ।ਜੇ ਕਦੇ ਕਾਲੇ ਚਟਾਕ ਦਿਖਾਈ ਦਿੰਦੇ ਹਨ, ਤਾਂ ਇਹ ਅੰਦਾਜ਼ਾ ਲਗਾਇਆ ਜਾਂਦਾ ਹੈ ਕਿ ਉਹਨਾਂ ਦਾ ਕਾਰਨ ਬੈਰਲ ਵਿੱਚ ਰਹਿਣ ਦੀ ਸੰਭਾਵਨਾ ਹੈ.ਇਸ ਲਈ, ਕਾਲੇ ਧੱਬੇ ਦਿਖਾਈ ਦੇਣ ਤੋਂ ਬਾਅਦ, ਵਿਰੋਧੀ ਉਪਾਅ ਕਰਨ ਤੋਂ ਪਹਿਲਾਂ ਬੈਰਲ ਨੂੰ ਚੰਗੀ ਤਰ੍ਹਾਂ ਸਾਫ਼ ਕੀਤਾ ਜਾਣਾ ਚਾਹੀਦਾ ਹੈ (ਨਹੀਂ ਤਾਂ ਕਾਲੇ ਧੱਬੇ ਕਦੇ ਵੀ ਅਲੋਪ ਨਹੀਂ ਹੋਣਗੇ)।
2. ਮੋਲਡਿੰਗ ਤਾਪਮਾਨ ਨੂੰ ਘੱਟ ਕਰਨ ਦੀ ਕੋਸ਼ਿਸ਼ ਕਰੋ
ਕਈ ਰੈਜ਼ਿਨਾਂ ਨੇ ਐਪਲੀਕੇਸ਼ਨ ਤਾਪਮਾਨਾਂ ਦੀ ਸਿਫਾਰਸ਼ ਕੀਤੀ ਹੈ (ਕੈਟਲਾਗ ਜਾਂ ਉਤਪਾਦ ਪੈਕੇਜ ਵਿੱਚ ਇਹ ਜਾਣਕਾਰੀ ਵੀ ਸ਼ਾਮਲ ਹੈ)।ਜਾਂਚ ਕਰੋ ਕਿ ਕੀ ਮੋਲਡਿੰਗ ਮਸ਼ੀਨ ਦਾ ਸੈੱਟ ਤਾਪਮਾਨ ਸੀਮਾ ਤੋਂ ਬਾਹਰ ਹੈ।ਜੇ ਅਜਿਹਾ ਹੈ, ਤਾਂ ਤਾਪਮਾਨ ਘਟਾਓ।ਇਸ ਤੋਂ ਇਲਾਵਾ, ਮੋਲਡਿੰਗ ਮਸ਼ੀਨ 'ਤੇ ਪ੍ਰਦਰਸ਼ਿਤ ਤਾਪਮਾਨ ਉਸ ਖੇਤਰ ਦਾ ਤਾਪਮਾਨ ਹੁੰਦਾ ਹੈ ਜਿੱਥੇ ਸੈਂਸਰ ਸਥਿਤ ਹੁੰਦਾ ਹੈ, ਜੋ ਅਸਲ ਰਾਲ ਦੇ ਤਾਪਮਾਨ ਤੋਂ ਕੁਝ ਵੱਖਰਾ ਹੁੰਦਾ ਹੈ।ਜੇ ਸੰਭਵ ਹੋਵੇ, ਤਾਂ ਰੈਸਿਨ ਥਰਮਾਮੀਟਰ ਜਾਂ ਇਸ ਤਰ੍ਹਾਂ ਦੇ ਨਾਲ ਅਸਲ ਤਾਪਮਾਨ ਨੂੰ ਮਾਪਣ ਦੀ ਸਿਫਾਰਸ਼ ਕੀਤੀ ਜਾਂਦੀ ਹੈ।ਖਾਸ ਤੌਰ 'ਤੇ, ਉਹ ਖੇਤਰ ਜੋ ਰਾਲ ਦੀ ਧਾਰਨਾ ਲਈ ਸੰਭਾਵਿਤ ਹੁੰਦੇ ਹਨ, ਜਿਵੇਂ ਕਿ ਚੈੱਕ ਰਿੰਗ, ਕਾਲੇ ਧੱਬਿਆਂ ਦਾ ਕਾਰਨ ਬਣਦੇ ਹਨ, ਇਸ ਲਈ ਆਲੇ ਦੁਆਲੇ ਦੇ ਤਾਪਮਾਨ ਵੱਲ ਵਿਸ਼ੇਸ਼ ਧਿਆਨ ਦਿਓ।
3. ਨਿਵਾਸ ਸਮਾਂ ਘਟਾਓ
ਭਾਵੇਂ ਮੋਲਡਿੰਗ ਮਸ਼ੀਨ ਦਾ ਸੈੱਟ ਤਾਪਮਾਨ ਵੱਖ-ਵੱਖ ਰੈਜ਼ਿਨਾਂ ਦੀ ਸਿਫ਼ਾਰਸ਼ ਕੀਤੀ ਤਾਪਮਾਨ ਸੀਮਾ ਦੇ ਅੰਦਰ ਹੋਵੇ, ਲੰਬੇ ਸਮੇਂ ਤੱਕ ਬਰਕਰਾਰ ਰੱਖਣ ਨਾਲ ਰਾਲ ਦੇ ਵਿਗੜ ਸਕਦੇ ਹਨ ਅਤੇ ਇਸ ਤਰ੍ਹਾਂ ਕਾਲੇ ਚਟਾਕ ਦਿਖਾਈ ਦੇ ਸਕਦੇ ਹਨ।ਜੇਕਰ ਮੋਲਡਿੰਗ ਮਸ਼ੀਨ ਦੇਰੀ ਸੈਟਿੰਗ ਵਿਸ਼ੇਸ਼ਤਾ ਦੀ ਪੇਸ਼ਕਸ਼ ਕਰਦੀ ਹੈ, ਤਾਂ ਕਿਰਪਾ ਕਰਕੇ ਇਸਦਾ ਪੂਰਾ ਫਾਇਦਾ ਉਠਾਓ, ਅਤੇ ਮੋਲਡਿੰਗ ਦੇ ਆਕਾਰ ਲਈ ਢੁਕਵੀਂ ਮੋਲਡਿੰਗ ਮਸ਼ੀਨ ਵੀ ਚੁਣੋ।
4. ਗੰਦਗੀ ਜਾਂ ਨਹੀਂ?
ਕਦੇ-ਕਦਾਈਂ ਹੋਰ ਰੈਜ਼ਿਨਾਂ ਜਾਂ ਧਾਤਾਂ ਦੇ ਮਿਸ਼ਰਣ ਦੇ ਨਤੀਜੇ ਵਜੋਂ ਕਾਲੇ ਧੱਬੇ ਵੀ ਹੋ ਸਕਦੇ ਹਨ।
ਹੈਰਾਨੀ ਦੀ ਗੱਲ ਇਹ ਹੈ ਕਿ ਇਸ ਦਾ ਕਾਰਨ ਜ਼ਿਆਦਾਤਰ ਨਾਕਾਫ਼ੀ ਸਫਾਈ ਹੈ।ਕਿਰਪਾ ਕਰਕੇ ਪਿਛਲੀ ਇੰਜੈਕਸ਼ਨ ਮੋਲਡਿੰਗ ਰਨ ਵਿੱਚ ਵਰਤੀ ਗਈ ਰਾਲ ਨੂੰ ਚੰਗੀ ਤਰ੍ਹਾਂ ਸਾਫ਼ ਕਰਨ ਅਤੇ ਹਟਾਉਣ ਤੋਂ ਬਾਅਦ ਕੰਮ ਕਰੋ।ਰੀਸਾਈਕਲ ਕੀਤੇ ਪਲਾਸਟਿਕ ਦੀ ਵਰਤੋਂ ਕਰਦੇ ਸਮੇਂ, ਇਹ ਦੇਖਣ ਲਈ ਨੰਗੀ ਅੱਖ ਨਾਲ ਜਾਂਚ ਕਰੋ ਕਿ ਕੀ ਗੋਲੀਆਂ ਵਿੱਚ ਵਿਦੇਸ਼ੀ ਪਦਾਰਥਾਂ ਦੀ ਮੌਜੂਦਗੀ ਹੈ।
ਪੋਸਟ ਟਾਈਮ: ਅਪ੍ਰੈਲ-11-2023